Arıza Türü ve Etki Analizinin Önemi
Şirketlerin ürün ve süreçlerinin büyük sorunlar yaşamadan çalışmasını nasıl sağladıklarını merak ediyor musunuz? FMEA diye bir şey kullanıyorlar. Yani FMEA, Arıza Modu ve Etkileri Analizi anlamına gelir. Birçok şirket, sorunları ortaya çıkmadan önce tespit etmek ve durdurmak için bunu kullanıyor. Daha derine inmek istiyorsanız bu kılavuzu okumaya devam edin. Gelin daha yakından bakalım FMEA nedirfarklı türleri de dahil olmak üzere. Ayrıca okumaya devam ederken nasıl çalıştığını ve nasıl kullanılacağını öğrenin. Son olarak, en iyi FMEA yapıcıyı keşfedin.
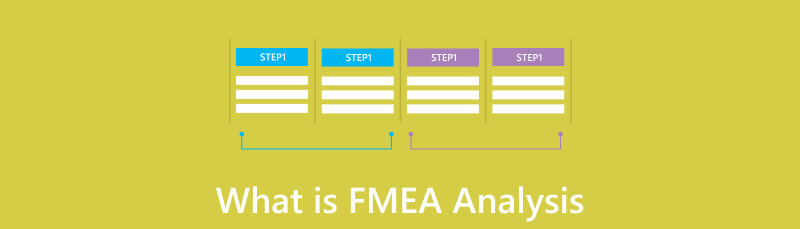
- Bölüm 1. FMEA Tanımı
- Bölüm 2. FMEA Türleri
- Bölüm 3. FMEA nasıl çalışır?
- Bölüm 4. FMEA Nasıl Kullanılır?
- Bölüm 5. FMEA Analizi Yapmak İçin En İyi Araç
- Bölüm 6. FMEA Analizi Nedir Hakkında SSS
Bölüm 1. FMEA Tanımı
FMEA nedir? FMEA, genellikle Ağaç Analizi olarak adlandırılan Arıza Modu ve Etkileri Analizi anlamına gelir. Bir bileşenin arızalanabileceği çeşitli modlarla bağlantılı potansiyel riskleri değerlendirmek için kullanılır. Ayrıca bu başarısızlıkların sonuçlarını tespit ederek gerektiğinde riskleri azaltacak bir çerçeve oluşturur. Başka bir şey de FMEA'nın yaygın olarak mühendislik değerlendirmesi olarak kullanılmasıdır. Çeşitli uzmanlardan oluşan bir ekip bunu yürütür. Geliştirmenin ilk aşamalarında ürün tasarımlarını veya üretim süreçlerini yakından incelerler. Bu analizin amacı, ürünlerin müşterinin eline ulaşmadan önce zayıf noktalarını tespit edip gidermektir. Aynı zamanda ürünün daha kaliteli ve güvenli olmasını da sağlar.
FMEA analizi örneğine bir göz atın. Aynı zamanda ilerledikçe görsel sunumun nasıl oluşturulduğunu da kontrol edin.
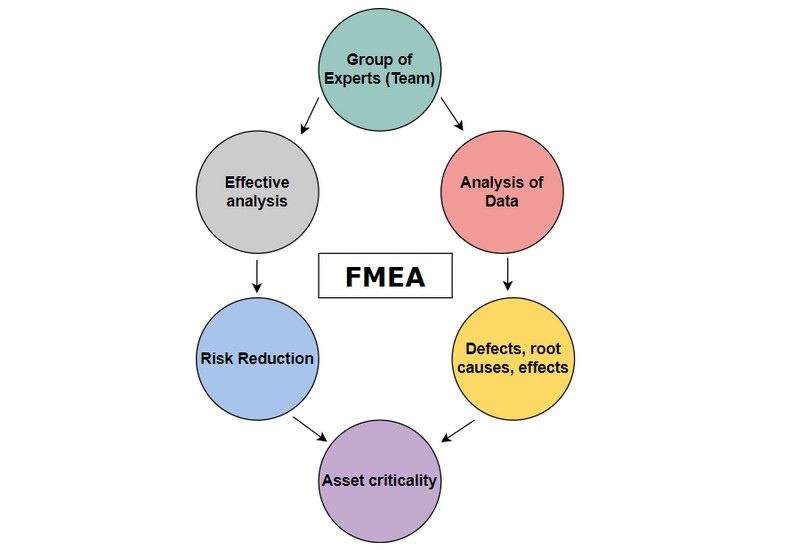
Ayrıntılı bir FMEA analizi edinin.
Bölüm 2. FMEA Türleri
Artık FMEA tanımını bildiğinize göre farklı türlerine geçebiliriz. FMEA'nın her biri biraz farklı odağa sahip üç ana türü vardır. Aşağıda okumaya devam ederken bu türleri tanıyın:
1. Tasarım FMEA (DFMEA)
Tasarım FMEA, planlama ve tasarım aşamalarında daha çok sistem veya ürüne odaklanır. DFMEA'daki ekipler, ürünün tasarımındaki olası sorunları bulmaya ve düzeltmeye çalışır. Kolayca kırılabilecek parçalar veya kullanıcıların kafasını karıştırabilecek özellikler içerir. Bir Tasarım FMEA'ya başladığınızda, öncelikle ürününüzün tüm farklı parçalarının bir listesini yaparsınız. Bu liste, tüm küçük parçaların dahil olduğu çok ayrıntılı olabilir. Ürün parçalara ayrıldıktan sonra her bir bileşenin olası arızalarını belirleyin. Bu türün amacı, ürünün en başından itibaren güvenli, güvenilir ve kullanımı kolay olmasını sağlamaktır.
2. Süreç FMEA'sı (PFMEA)
Süreç FMEA'sı işlerin nasıl yapıldığını analiz etmek ve sürdürmekle ilgilidir. PFMEA'da, DFMEA'dan farklı olarak ürünün kendisi üzerinde çalışan bir süreç üzerinde gerçekleştirilir. Ayrıca PFMEA Çalışma Sayfasının ilk sütunlarında sürecinizin adımlarını listelemelisiniz. Ürününüzün DFMEA'daki bileşenleriyle karşılaştırıldığında. Burada ekip, hizmet veya üretim süreçlerindeki sorunları aramaya odaklanır. Bu sorunların ne kadar muhtemel olduğunu ve ne kadar kötü olabileceğini anlamaya çalışırlar. Daha sonra bunları önlemenin veya düzeltmenin yollarını bulurlar.
3. Sistem FMEA'sı (SFMEA)
Adından da anlaşılacağı gibi SFMEA sistemle ilgili sorunlara odaklanmıştır. Aynı zamanda fonksiyonel FMEA veya FFMEA olarak da adlandırılır. Yani bu analiz tüm sisteme yüksek oranda bakıyor. SFMEA'daki ekipler, farklı parçalar veya sistemler arasındaki etkileşimleri ve bağlantıları analiz eder. Bir parçadaki arızanın tüm sistemi nasıl etkileyebileceğini anlamak istiyorlar. Aynı şekilde bu riskleri nasıl en aza indireceklerini de bilmeleri gerekiyor. Başka bir deyişle System FMEA, daha büyük süreçlerde veya projelerde tüm parçaların birlikte iyi çalışmasını sağlar.
Bölüm 3. FMEA Nasıl Çalışır?
Neyin Yanlış Gidebileceğini Belirleyin
İlk olarak bir ekip, yanlış gidebilecek her şeyin bir listesini yapmak için toplanır. Süreçte, üründe veya sistemde olabilir. Hatalar veya aksilikler ne kadar küçük veya büyük olursa olsun hepsini tespit edersiniz.
Ciddiyeti Değerlendirin
Olası sorunlar ortaya çıkarsa ekip bunun ne kadar kötü olabileceğini düşünür ve değerlendirir. Ayrıca her soruna, sorunun ne kadar ciddi olduğunu göstermek için bir puan verirler. Bu şekilde en önemli sorunlara odaklanmalarına yardımcı olur.
Olasılığa Karar Ver
Ekip artık her sorunun ne kadar muhtemel olduğunu hesaplıyor. Ekip bunun gerçekleşme olasılığını tahmin etmek için bir derecelendirme kullanacak. Böylece nelere dikkat edilmesi gerektiğini önceliklendirmeye yardımcı olur.
Sebepleri Belirleyin
Ekip, her sorun için bunun neden olabileceğini bulmaya çalışır. Ekip, bir arabanın neden bozulabileceği (örneğin, yağın az olması) gibi ana nedeni arıyor.
Önleyici Yöntemler Oluşturun
Tüm bilgilere sahip olan ekip, bu sorunları önlemek için beyin fırtınası yapacaktır. Aynı zamanda stratejiler veya planlar oluştururlar. Örneklerden biri, arabanın arızalanmasını önlemek için yağın düzenli olarak kontrol edilmesidir.
Yeniden Değerlendirin ve İyileştirin
Son olarak ekip zaman içinde olaylara göz kulak olacak. Daha sonra önleyici faaliyetlerin işe yaradığından emin olurlar. Yeni sorunlar ortaya çıkarsa veya eski sorunlar düzelmiyorsa çizim tahtasına geri dönerler. Oradan iyileştirmeler yapacaklar.
Bölüm 4. FMEA Nasıl Kullanılır?
Arıza Modu ve Etki Analizi'ni (FMEA) kullanarak sorunları önlemek için bir güvenlik planı oluşturabilirsiniz. FMEA'nın nasıl kullanılacağına dair basit bir kılavuz:
1. Bir Ekip Toplayın
Öncelikle bir grup insanı toplayın. Ekibinizin analiz etmek istediğiniz süreci, ürünü veya sistemi bilmesi gerekir.
2. Olası Sorunları Belirleyin
Bu adımda ters gidebilecek her şeyi listeleyerek başlayın. Oluşabilecek sorunları listeleyin ve tanımlayın.
3. Sorunları Değerlendirin
Listelediğiniz her sorun için, gerçekleşmesi durumunda ne kadar kötü olacağını düşünün. 1'in o kadar da kötü olmadığı ve 10'un gerçekten çok kötü olduğu 1'den 10'a kadar bir ölçek kullanın. Bu, hangi sorunların en ciddi olduğunu anlamanıza yardımcı olur.
4. Olasılığı Değerlendirin
Daha sonra, her bir sorunun ortaya çıkma olasılığını tahmin edin. Her konuya bir olasılık puanı verin.
5. Sebepleri Tespit Edin
Her sorunun neden olabileceğini anlamaya çalışın. Son kullanma tarihi geçmiş malzemeleri kullanma konusunda endişeleniyorsanız bunun nedeni son kullanma tarihlerini kontrol etmemiş olmanız olabilir.
6. Önleyici Faaliyetler için Beyin Fırtınası Yapın
Şimdi bu sorunları önlemenin veya daha az kötü hale getirmenin yollarını beyin fırtınası yapın.
7. Risk Önceliğini Hesaplayın
Her problem için ciddiyet puanını olasılık puanıyla çarpın. Bu size bir “Risk Öncelik Numarası” veya RPN verir. RPN ne kadar yüksek olursa, bu sorunla baş etmek o kadar acil olur.
8. Yüksek RPN'lere Odaklanın
En yüksek RPN'lere sahip sorunlara özellikle dikkat edin. Bunlar en acil eyleme ihtiyaç duyanlardır.
9. Uygulama ve İzleme
Önleyici eylemlerinizi uygulamaya koyun. Çalışıp çalışmadıklarını görmek için şeylere göz kulak olun. Sorunlar hâlâ devam ediyorsa planınızı düzenleyin ve başka bir şey deneyin.
10. Düzenli Olarak İnceleyin ve İyileştirin
FMEA tek seferlik bir şey değildir. Planınızı zaman içinde gözden geçirmeye ve geliştirmeye devam edin. Daha fazlasını öğrendikçe daha da iyi hale getirebilirsiniz.
Bölüm 5. FMEA Analizi Yapmak İçin En İyi Araç
MindOnMap üst düzey bir FMEA (Arıza Modu ve Etki Analizi) üreticisidir. İşletmeler ve kuruluşlar için güçlü ve kullanımı kolay bir platform sunar. Aynı zamanda risk yönetimi ve kalite iyileştirmede mükemmelliği aramak için de en iyi araçtır. MindOnMap ile FMEA sürecini basitleştirmek ve kolaylaştırmak için tasarlanmış kapsamlı bir çözüm bulacaksınız. MindOnMap'i en iyi FMEA oluşturucu olarak diğerlerinden ayıran şey sezgisel arayüzüdür. Hem yeni başlayanlar hem de profesyoneller bu aracı kullanmaktan keyif alabilirler. Üstelik ekiplerin birlikte çalışması için kusursuz bir deneyim sunuyor. Herkesin kendi uzmanlık ve içgörüleriyle katkıda bulunabilmesini sağlar.
İster potansiyel arıza modlarını tanımlıyor, ister etkilerini değerlendiriyor olun, vb., MindOnMap size mükemmelleşmeniz için gereken rehberliği sağlar. Bununla birlikte riskleri proaktif bir şekilde ele alma, ürün kalitesini artırma ve operasyonel verimliliği optimize etme konusunda güvene sahip olacaksınız. Bu nedenle FMEA analizinde mükemmelliğe ulaşmaya kararlı olanların ilk tercihidir.
Güvenli indirme
Güvenli indirme
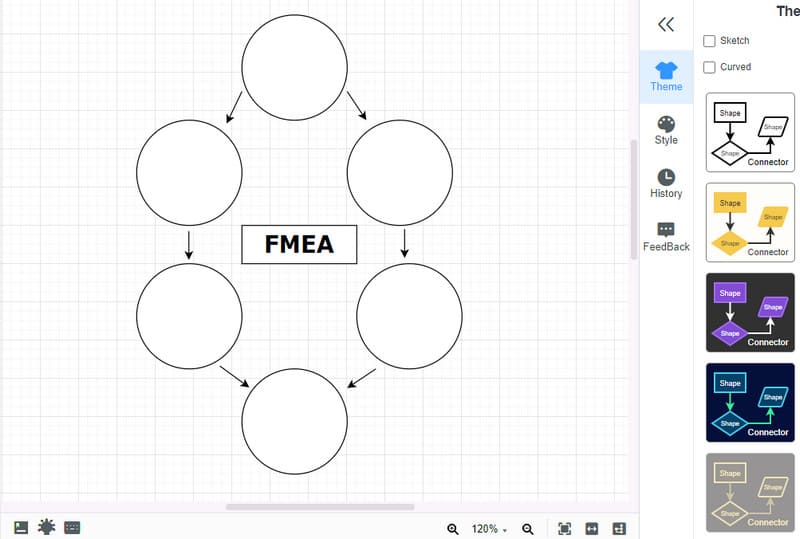
Daha fazla okuma
Bölüm 6. FMEA Analizi Nedir Hakkında SSS
FMEA sürecinin 5 adımı nedir?
FMEA sürecinin 5 adımı şunlardır:
1. Olası sorunları tanımlayın.
2. Bu sorunların ciddiyetini derecelendirin.
3. Sorunların ortaya çıkma olasılığını tahmin edin.
4. Bu sorunların nedenlerini bulun.
5. Sorunları önlemek veya yönetmek için planlar geliştirin.
FMEA'nın bir örneği nedir?
Bir araba üretim süreci bağlamında FMEA örneğini ele alalım: İlk olarak, motorun aşırı ısınması ve boya kusurları gibi olası sorunları tanımlayın. Daha sonra bunların ciddiyetini ve olasılığını değerlendirin. Daha sonra hatalı termostat veya insan hatası gibi nedenleri arayın. Şimdi tasarım iyileştirmeleri ve daha iyi kalite kontrolü gibi planlar geliştirin. Böylece bu sorunları önleyecek ve aksiyonlara öncelik vereceksiniz.
FMEA yalın mı yoksa Altı Sigma mı?
FMEA, Altı Sigma metodolojisinde yaygın olarak kullanılan bir araçtır. Özellikle Yalın veya Altı Sigma'nın bir parçası değildir. Ancak sıklıkla bu kalite iyileştirme yaklaşımlarına dahil edilir.
Çözüm
Sonuç olarak, tanımını ve türlerini öğrendiniz. FMEA analizi, nasıl çalıştığı ve nasıl kullanılacağı. Gerçekten de FMEA, endüstriler genelinde ürün kalitesini, güvenilirliğini ve güvenliğini arttırmada önemli bir rol oynamaktadır. Kuruluşlar etkili FMEA çözümleri ararken, MindOnMap En iyi FMEA üreticilerinden biri olarak öne çıkıyor. Basit arayüzü ve güçlü özellikleriyle kullanıcılar istedikleri FMEA diyagramını yapabilmelerini sağlayabilirler.