اهمیت حالت شکست و تجزیه و تحلیل اثرات
آیا میپرسید چگونه شرکتها مطمئن میشوند که محصولات و فرآیندهایشان بدون هیچ مشکل بزرگی کار میکنند؟ خوب، آنها از چیزی به نام FMEA استفاده می کنند. بنابراین، FMEA مخفف Failure Mode and Effects Analysis است. بسیاری از شرکت ها از آن برای شناسایی و توقف مشکلات قبل از وقوع استفاده می کنند. اگر می خواهید عمیق تر شوید، به خواندن این راهنما ادامه دهید. بیایید نگاهی دقیق تر بیندازیم FMEA چیست، از جمله انواع مختلف آن. همچنین، در ادامه خواندن، یاد بگیرید که چگونه کار می کند و چگونه از آن استفاده کنید. در نهایت، سازنده برتر FMEA را کشف کنید.
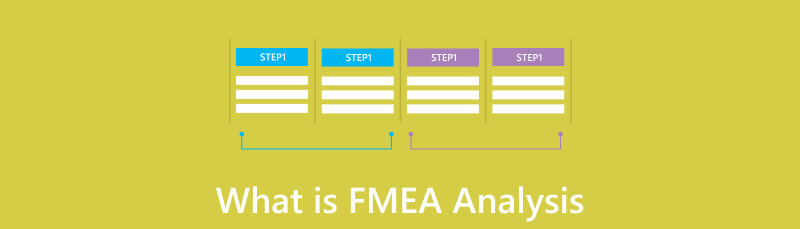
- قسمت 1. تعریف FMEA
- قسمت 2. انواع FMEA
- قسمت 3. چگونه FMEA کار می کند
- قسمت 4. نحوه استفاده از FMEA
- بخش 5. بهترین ابزار برای انجام تجزیه و تحلیل FMEA
- بخش 6. سوالات متداول در مورد تجزیه و تحلیل FMEA چیست
قسمت 1. تعریف FMEA
FMEA چیست؟ FMEA به معنای تجزیه و تحلیل حالت شکست و اثرات است که اغلب به آن تجزیه و تحلیل درختی می گویند. برای ارزیابی ریسکهای بالقوه مرتبط با حالتهای مختلف که در آن یک جزء ممکن است از کار بیفتد استفاده میشود. همچنین پیامدهای این شکست ها را شناسایی می کند و چارچوبی برای کاهش ریسک ها در مواقع لزوم ایجاد می کند. چیز دیگر، FMEA معمولا به عنوان یک ارزیابی مهندسی استفاده می شود. یک تیم متنوع از کارشناسان آن را انجام می دهند. آنها طرح های محصول یا فرآیندهای تولید را در مراحل اولیه توسعه به دقت بررسی می کنند. هدف از این تحلیل شناسایی و رفع نقاط ضعف محصولات قبل از رسیدن به دست مشتری است. در عین حال کیفیت و ایمنی بالاتر محصول را نیز تضمین می کند.
به نمونه ای از تجزیه و تحلیل FMEA نگاه کنید. در همان زمان، بررسی کنید که چگونه ارائه بصری ایجاد می شود.
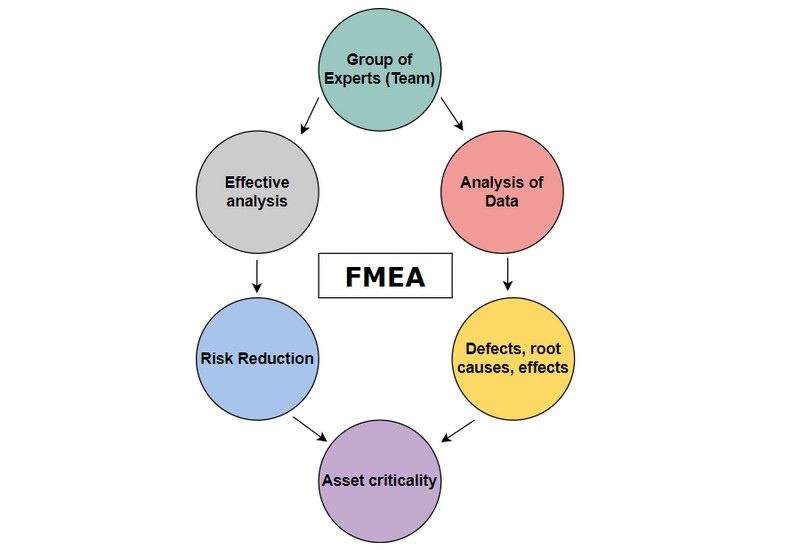
تجزیه و تحلیل دقیق FMEA را دریافت کنید.
قسمت 2. انواع FMEA
اکنون که تعریف FMEA را دارید، به انواع مختلف آن می پردازیم. FMEA دارای سه نوع اصلی است که هر کدام تمرکز کمی متفاوت دارند. با ادامه خواندن زیر، با این انواع آشنا شوید:
1. طراحی FMEA (DFMEA)
طراحی FMEA در مراحل برنامه ریزی و طراحی بیشتر بر روی سیستم یا محصول متمرکز است. تیمهای موجود در DFMEA سعی میکنند هر گونه مشکل احتمالی را در طراحی محصول پیدا کرده و برطرف کنند. این شامل قطعاتی است که ممکن است به راحتی شکسته شوند یا ویژگی هایی که ممکن است برای کاربران گیج کننده باشد. هنگامی که یک Design FMEA را راه اندازی می کنید، ابتدا لیستی از تمام بخش های مختلف محصول خود تهیه می کنید. این لیست می تواند بسیار دقیق باشد، با تمام قطعات کوچک. هنگامی که محصول به قطعات تقسیم شد، خرابی های احتمالی هر جزء را مشخص کنید. هدف از این نوع اطمینان از ایمنی، قابل اعتماد بودن و استفاده آسان محصول از ابتدا است.
2. فرآیند FMEA (PFMEA)
فرآیند FMEA در مورد تجزیه و تحلیل و حفظ نحوه انجام کارها است. در PFMEA، بر خلاف DFMEA که روی خود محصول کار می کند، بر روی یک فرآیند انجام می شود. علاوه بر این، در ستون های اولیه کاربرگ PFMEA، باید مراحل فرآیند خود را فهرست کنید. در مقایسه با اجزای محصول شما در DFMEA. در اینجا، تیم بر جستجوی مشکلات در خدمات یا فرآیندهای تولید تمرکز می کند. آنها سعی می کنند بفهمند این مشکلات چقدر محتمل هستند و چقدر می توانند بد باشند. سپس راه هایی برای پیشگیری یا رفع آن ها ارائه می کنند.
3. سیستم FMEA (SFMEA)
همانطور که از نام آن پیداست، SFMEA بر مشکلات مربوط به سیستم متمرکز است. به آن FMEA عملکردی یا FFMEA نیز می گویند. بنابراین، این تحلیل به شدت به کل سیستم نگاه می کند. تیم های SFMEA تعاملات و ارتباطات بین بخش ها یا سیستم های مختلف را تجزیه و تحلیل می کنند. آنها می خواهند بفهمند که چگونه یک شکست در یک بخش می تواند کل سیستم را تحت تاثیر قرار دهد. به همین ترتیب، آنها باید بدانند که چگونه این خطرات را به حداقل برسانند. به عبارت دیگر، System FMEA تضمین می کند که تمام قطعات در فرآیندها یا پروژه های بزرگتر به خوبی با هم کار می کنند.
قسمت 3. چگونه FMEA کار می کند
تشخیص دهید چه چیزی می تواند اشتباه باشد
ابتدا یک تیم جمع می شود تا لیستی از همه چیزهایی که ممکن است اشتباه پیش برود تهیه کنند. ممکن است در فرآیند، محصول یا سیستم باشد. مهم نیست اشتباهات یا بدبختی ها چقدر کوچک یا بزرگ، همه آنها را شناسایی می کنید.
به جدیت امتیاز دهید
اگر مشکلات احتمالی ممکن است رخ دهد، تیم فکر میکند و ارزیابی میکند که چقدر میتواند بد باشد. آنها همچنین برای هر مشکل نمره ای برای نشان دادن میزان جدی بودن آن ارائه می کنند. به این ترتیب، به آنها کمک می کند تا روی مهم ترین مشکلات تمرکز کنند.
احتمال تصمیم گیری کنید
اکنون، تیم متوجه می شود که احتمال وقوع هر مشکل چقدر است. تیم از یک رتبه بندی برای تخمین احتمال وقوع آن استفاده خواهد کرد. بنابراین، به اولویت بندی آنچه باید توجه شود کمک می کند.
علل را تعیین کنید
برای هر مشکل، تیم تلاش میکند تا دریابد که چرا ممکن است اتفاق بیفتد. تیم به دنبال دلیل اصلی است، مانند اینکه چرا یک ماشین ممکن است خراب شود (مثلاً روغن کم).
روش های پیشگیری را ایجاد کنید
تیم با در اختیار داشتن تمام اطلاعات، ایده هایی را برای جلوگیری از این مشکلات مطرح می کند. در عین حال، آنها استراتژی ها یا برنامه هایی را ایجاد می کنند. یکی از مثالها بررسی منظم روغن برای جلوگیری از خرابی خودرو است.
ارزیابی مجدد و بهبود
در نهایت، تیم به مرور زمان همه چیز را زیر نظر خواهد داشت. سپس، آنها مطمئن می شوند که اقدامات پیشگیرانه موثر هستند. اگر مشکلات جدید اتفاق بیفتد یا مشکلات قدیمی بهتر نشدند، به تابلوی نقاشی برمیگردند. از آنجا، آنها پیشرفت هایی را انجام خواهند داد.
قسمت 4. نحوه استفاده از FMEA
با استفاده از حالت شکست و تجزیه و تحلیل اثرات (FMEA)، می توانید یک طرح ایمنی برای جلوگیری از مشکلات ایجاد کنید. در اینجا یک راهنمای ساده در مورد نحوه استفاده از FMEA آورده شده است:
1. یک تیم جمع کنید
ابتدا یک گروه از افراد را جمع کنید. تیم شما باید فرآیند، محصول یا سیستمی را که می خواهید تجزیه و تحلیل کنید، بداند.
2. مشکلات احتمالی را شناسایی کنید
در این مرحله، با فهرست کردن همه مواردی که ممکن است اشتباه کنند، شروع کنید. مواردی را که ممکن است رخ دهد فهرست کرده و شناسایی کنید.
3. به مشکلات امتیاز دهید
برای هر مشکلی که فهرست کردید، به این فکر کنید که اگر اتفاق بیفتد چقدر بد خواهد بود. از مقیاسی مانند 1 تا 10 استفاده کنید که 1 چندان بد نیست و 10 واقعاً بسیار بد است. این به شما کمک می کند بفهمید کدام مشکلات جدی ترین هستند.
4. به Possibility امتیاز دهید
در مرحله بعد، احتمال وقوع هر مشکل را تخمین بزنید. به هر شماره یک امتیاز امکان بدهید.
5. تشخیص علل
سعی کنید بفهمید چرا هر مشکلی ممکن است اتفاق بیفتد. اگر نگران استفاده از مواد منقضی شده هستید، علت ممکن است این باشد که تاریخ انقضا را بررسی نکرده اید.
6. اقدامات پیشگیرانه طوفان فکری
اکنون، راههایی را برای جلوگیری از این مشکلات یا کاهش بدتر کردن آنها بنویسید.
7. محاسبه اولویت ریسک
نمره جدیت را در امتیاز احتمال برای هر مشکل ضرب کنید. این به شما یک "شماره اولویت ریسک" یا RPN می دهد. هر چه RPN بالاتر باشد، مقابله با آن مشکل ضروری تر است.
8. روی RPN های بالا تمرکز کنید
به مشکلات بالاترین RPN توجه ویژه ای داشته باشید. اینها کسانی هستند که نیاز به اقدام فوری دارند.
9. اجرا و نظارت
اقدامات پیشگیرانه خود را عملی کنید. مراقب چیزها باشید تا ببینید کار می کنند یا خیر. اگر مشکلات همچنان در حال رخ دادن هستند، برنامه خود را تنظیم کنید و چیز دیگری را امتحان کنید.
10. به طور منظم مرور و بهبود دهید
FMEA چیزی یکبار مصرف نیست. به مرور و بهبود برنامه خود در طول زمان ادامه دهید. همانطور که بیشتر یاد می گیرید، می توانید آن را حتی بهتر کنید.
بخش 5. بهترین ابزار برای انجام تجزیه و تحلیل FMEA
MindOnMap یک سازنده رده بالا FMEA (تحلیل حالت و اثرات شکست) است. این یک پلت فرم قدرتمند و آسان برای کار برای مشاغل و سازمان ها ارائه می دهد. همچنین بهترین ابزار برای جستجوی برتری در مدیریت ریسک و بهبود کیفیت است. با MindOnMap، راه حل جامعی خواهید یافت که برای ساده سازی و ساده سازی فرآیند FMEA طراحی شده است. چیزی که MindOnMap را به عنوان بهترین سازنده FMEA متمایز می کند، رابط بصری آن است. هم مبتدیان و هم حرفه ای ها ممکن است از استفاده از این ابزار لذت ببرند. علاوه بر این، تجربه یکپارچه ای را برای تیم ها برای همکاری با یکدیگر ارائه می دهد. این تضمین می کند که همه می توانند تخصص و بینش خود را به اشتراک بگذارند.
اکنون، چه در حال شناسایی حالتهای شکست بالقوه، ارزیابی تأثیرات آنها و غیره باشید، MindOnMap راهنمایی لازم برای برتری را ارائه میکند. با آن، اعتماد به نفس لازم برای مقابله فعالانه با خطرات، افزایش کیفیت محصول و بهینه سازی کارایی عملیاتی را خواهید داشت. به همین دلیل است که برای کسانی که متعهد به دستیابی به برتری در تجزیه و تحلیل FMEA هستند، انتخابی مناسب است.
دانلود امن
دانلود امن
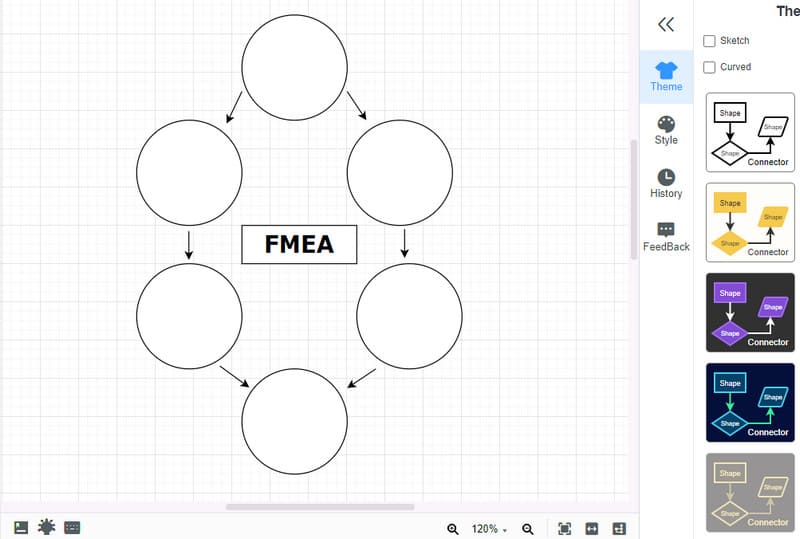
بیشتر خواندن
بخش 6. سوالات متداول در مورد تجزیه و تحلیل FMEA چیست
5 مرحله فرآیند FMEA چیست؟
5 مرحله فرآیند FMEA عبارتند از:
1. مشکلات احتمالی را شناسایی کنید.
2. جدی بودن آن مشکلات را ارزیابی کنید.
3. احتمال وقوع مشکلات را برآورد کنید.
4. علل این مشکلات را بیابید.
5. برای پیشگیری یا مدیریت مشکلات برنامه ریزی کنید.
نمونه ای از FMEA چیست؟
بیایید مثالی از FMEA را در زمینه فرآیند تولید خودرو در نظر بگیریم: ابتدا، مسائل بالقوه مانند داغ شدن بیش از حد موتور و نقص رنگ را شناسایی کنید. سپس، جدیت و احتمال آنها را ارزیابی کنید. در مرحله بعد، به دنبال علل، مانند خرابی ترموستات یا خطای انسانی باشید. اکنون، طرح هایی مانند بهبود طراحی و کنترل کیفیت بهتر را توسعه دهید. به این ترتیب، از این مشکلات جلوگیری می کنید و اقدامات را در اولویت قرار می دهید.
آیا FMEA ناب است یا شش سیگما؟
FMEA ابزاری است که معمولاً در متدولوژی شش سیگما استفاده می شود. این به طور خاص بخشی از ناب یا شش سیگما نیست. با این حال، اغلب در این رویکردهای بهبود کیفیت گنجانده می شود.
نتیجه
برای نتیجه گیری، شما با تعریف و انواع آن آشنا شده اید تجزیه و تحلیل FMEA، نحوه کارکرد و نحوه استفاده از آن. در واقع، FMEA نقش اساسی در افزایش کیفیت، قابلیت اطمینان و ایمنی محصول در سراسر صنایع ایفا می کند. همانطور که سازمان ها به دنبال راه حل های موثر FMEA هستند، MindOnMap به عنوان یکی از بهترین سازندگان FMEA متمایز است. با رابط ساده و ویژگی های قدرتمند آن، کاربران می توانند اطمینان حاصل کنند که می توانند نمودار FMEA مورد نظر خود را ایجاد کنند.