Figure Out and Understand the Difference Between FMEA & FMECA
In a world of analyzing risks, FMEA and FMECA are two of the most important tools. FMEA means Failure Mode and Effect Analysis. While FMECA stands for Failure Modes, Effects, and Criticality Analysis. They are systematic methods used to identify failures in products, processes, or systems. While both methodologies share common goals, they differ in depth and complexity. In this comprehensive review, we'll delve into the distinctions between FMECA and FMEA. Moreover, get to know the top-notch tool to make FMEA and FMECA analyses.
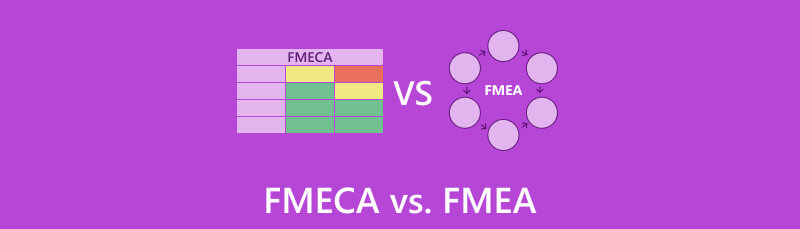
- Part 1. What is FMECA
- Part 2. What is FMEA
- Part 3. FMECA vs. FMEA
- Part 4. Best Tool to Do FMEA & FMECA Analysis
- Part 5. FAQs About FMECA vs. FMEA
Part 1. What is FMECA
FMECA stands for Failure Modes, Effects, and Criticality Analysis. It checks and manages potential failures in systems, products, or processes. It also builds upon the principles of Failure Modes and Effects Analysis (FMEA). Not only failure modes, causes, and effects but also their criticality and consequences. FMECA analysis aims to focus on the most critical failure modes. It means those that could have severe impacts on safety, performance, or other aspects. Besides, it evaluates factors such as likelihood, severity, and detectability. By doing so, FMECA helps organizations assign more resources to address high-risk issues.
You may also check out the diagram examples below.
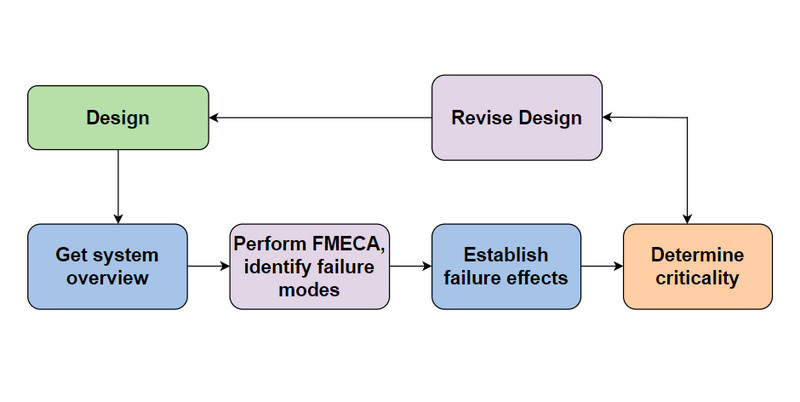
Part 2. What is FMEA
FMEA, or Failure Modes and Effects Analysis, identifies potential failure modes. It involves breaking down the system into its components. Then, understanding component failure possibilities and evaluating their consequences. FMEA assigns a risk priority number (RPN) to each failure mode. Each failure mode depends on its severity, occurrence likelihood, and detectability. This prioritization helps organizations focus on addressing the most critical issues first. By identifying and alleviating risks, FMEA enhances product reliability, safety, and quality. It is a valuable tool for preventing problems, reducing defects, and improving performance. With that, FMEA is an essential part of quality management risk reduction.
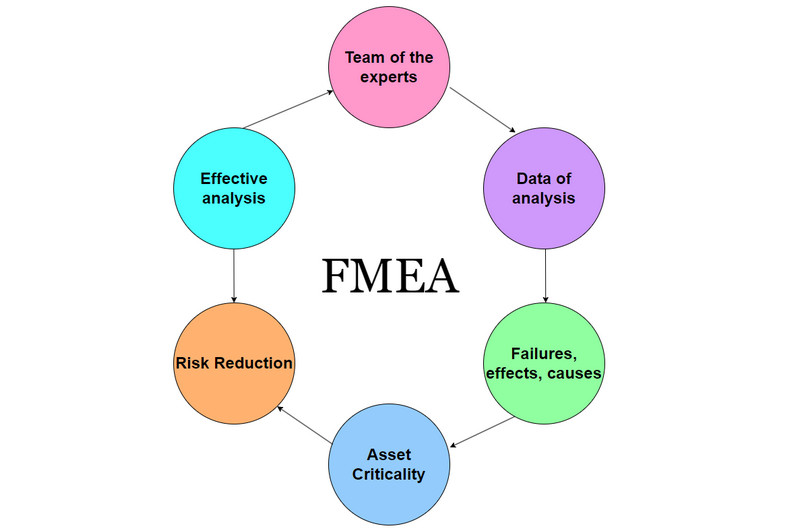
Part 3. FMECA vs. FMEA
FMECA and FMEA are both used in risk assessment and failure analysis. Although they are almost related, they have distinct differences:
1. Depth of Analysis
FMEA: Only focuses on identifying and assessing potential failure modes, causes, and effects. It provides a systematic framework for understanding what could go wrong.
FMECA: FMECA builds upon FMEA by adding criticality assessment. Besides failure modes, it evaluates their potential impact on the system or process. This added step helps to identify between failure modes with degrees of severity.
2. Criticality Assessment
FMEA: This analysis doesn't assign a criticality value to each failure mode. Instead, it treats all identified failure modes as equal. Thus, it may not distinguish between critical and less critical issues.
FMECA: It evaluates the criticality of each failure mode. It assesses likelihood, impact severity, and detectability of failures to determine their criticality. This assessment allows for a clear prioritization of risks.
3. Complexity and Use Cases
FMEA: This is well-suited for simple systems, processes, or products. Some industries use it where a detailed criticality assessment is not essential.
FMECA: It is for complex systems or high-risk environments. Also, where understanding the criticality of failures is important.
4. Resource Allocation
FMEA: The absence of criticality assessment may not guide resource allocation for FMEA. This is because all identified failure modes are being treated the same. Thus, it may lead to misallocation of resources and efforts.
FMECA: FMECA's criticality assessment allows for more efficient resource allocation. It ensures that they address the most critical and high-impact risks. So, it helps organizations focus their resources where they are most needed.
5. Industry Application
FMEA: FMEA is being used in many different industries. It includes making things for regular people, electronics, and basic manufacturing. These are places where you don't always need to look deeper into how bad things could get if they break.
FMECA: FMECA is being used in complex and super-important areas. It includes airplanes, hospitals, the army, and car-making. In these places, it's indeed important to know how bad things could get if they go wrong. Because the results could be very, very bad.
Part 4. Best Tool to Do FMEA & FMECA Analysis
Are you looking for a tool to streamline your FMEA or FMECA analysis? MindOnMap is the right FMEA and FMECA tool for you.
It is a versatile platform that lets you enhance the process of conducting analysis. A web-based tool that you can access on popular browsers like Google Chrome, Safari, Edge, and more. Also, it has a downloadable app version that supports Windows and Mac OS. What's more, it offers tons of diagram editing functions. With it, you can add shapes, text boxes, color fills, pictures, links, and so on. You can also create a treemap, fishbone diagram, organizational chart, etc., using it. One of the best features of this FMEA and FMECA software is the collaboration feature. Thus allowing you to collaborate on your work with your friends and colleagues. At the same time, share more ideas in real time.
Another notable thing is its auto-save feature. It allows you to save your editing after you stop operating on the tool. Thus, it prevents you from preventing any essential details in your analysis diagram. To start your analysis journey and experience the tool’s capabilities, try it now!
Secure Download
Secure Download
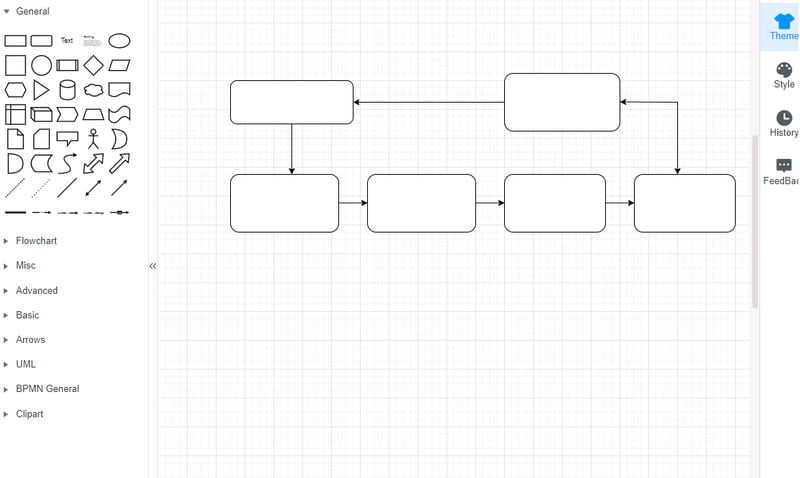
Further Reading
Part 5. FAQs About FMECA vs. FMEA
What is a FMECA used for?
Industries use FMECA to assess potential failures in complex systems, products, or processes. It goes beyond standard FMEA by considering the criticality of failure modes. Then, assessing their impact, likelihood, and detectability.
What is the difference between FMEA and FMA?
The key difference between FMEA and FMA is that FMEA is a comprehensive method. FMEA assesses not only failure modes but also their causes and effects. Thus aiming to identify and focus on potential issues. While FMA focuses on understanding failure modes and their characteristics without considering causes.
What is the difference between FMEA and FMEDA?
FMEA and FMEDA differ in their scope and purpose. Companies use FMEA to identify potential failure modes. Then, assessing their effects without addressing diagnostic aspects. In contrast, FMEDA concentrates on the diagnostic capability of a system. It focuses on the likelihood of detecting a failure before it causes harm or disruption.
Conclusion
To wrap it up, you have learned both the FMEA and FMECA definition and their differences. Indeed, these two are indispensable tools for risk management and quality improvement. The choice between FMEA and FMECA depends on the requirements of a project and the industry. Applying these methods ensures everything meets high standards of quality and safety. If you’re also in search of FMEA and FMECA tools to assist you, MindOnMap is the one. It is an all-in-one diagram maker that has editing, collaboration, and auto-saving features.